Underground Storage Tank (UST) Removal Project
Recently, we completed an Underground Storage Tank (UST) removal and soil remediation project in New Jersey and thought it might be of value to share our process and expertise to provide insight on how we consistently complete challenging projects for our clients with a smile and a high level of integrity.
THE PROJECT
During initial conversations with the client we firmly understood that this would be an interesting and challenging project but one where our experience would allow us to shine and create a positive outcome. The site was a former commercial bus depot and the 10,000 gallon UST was originally assumed to be constructed of fiberglass. However, when we arrived on site and began the work, we immediately identified that the UST was constructed of steel and not fiberglass. The weight of the steel tank - they’re often around 4 times the weight of their fiberglass counterparts – meant that the project approach was going to need to be changed. Fortunately, we’re a dynamic firm that thrives on adapting to change and taking on challenging projects. In fact, we gained a strong reputation early on for accepting jobs that other firms either couldn’t figure out or deemed “too difficult”. For us, it was just another great day of “Challenge accepted!” and we knew we were going to create a great experience for the client.
OUR PROCESS
Accessing & Cleaning the UST
Before breaking ground, we secured all necessary State and local permits and completed a public utility mark out as required by law through the New Jersey One Call notification system. The New Jersey One Call system only marks public utilities and as there was significant potential of encountering private utilities in the work area, we contracted with a private utility locating company to complete a geophysical investigation. This firm identified the boundary of the UST as well as other potential unmarked utilities and subsurface fixtures. As part of our company commitment to the safety of our clients, crews and the surrounding areas we work in, we always take that extra step to make sure any potential safety issues are unidentified before any work begins.
Once all pre-mobilization permitting, utility location, and general site safety checklists were completed, we utilized our excavation equipment to uncover the top of the UST in order to gain safe access for the removal of bulk liquids and tank entry for cleaning work. We initially removed fittings on the exposed portion of the tank and utilized our vacuum truck to remove the remaining free liquids. Once complete, we utilized and LEL meter to check the tank for potentially life threatening hazards such as a lack of oxygen or explosive atmosphere and completed purging and inerting as needed to ensure it was safe to cut open and enter the tank for cleaning. A confined space entry retrieval system was set up and while continuously monitoring the tank atmosphere the tank was entered & cleaned. Once cleaning was complete, the UST was ready for removal.
Removal
Before removing a tank from the ground, the soils surrounding it need to be excavated so the tank can be safely removed. Once the cleaned tank is removed from the excavation, it can then be transported off-site to a recycling facility for processing and beneficial reuse, which is one benefit of steel tanks. As many tanks as we have removed during our 27 years in business, I always wondered if they come back as cars, refrigerators or countless other useful items after the recycling process but I guess we will never know. The downside to using steel tanks is that they are very susceptible to rust and corrosion, which potentially leads large scale environmental impacts and public health issues.
Soil Remediation
Once the UST was removed, the tank carcass is inspected for evidence of corrosions holes, seam failures and general age-related decay that indicates a potential release may have occurred. Additionally, the bottom and sidewalls of the excavation are inspected for any evidence of a discharge such as soil staining or petroleum odors that might indicate a potential impact to the surrounding soils. In this case, the client already completed a soil investigation and determined that a release had in fact occurred and soil contamination was identified outside the footprint of the UST. Having this information available prior to initiating the tank removal activities allowed us to be well prepared to complete the required remedial activities in the most cost-effective manner.
We immediately removed and stockpiled contaminated soils, stockpiling it on and covering it with heavy plastic sheeting. Once all of the impacted soils were removed and staged, the next step was to load the impacted soils and transport the material to an approved and properly permitted facility for disposal and beneficial reuse. As the impacted soils were being transported off-site for disposal, certified clean fill material was delivered to the site and used to backfill the excavation. During the backfilling process, we mechanically compacted the fill material to prevent future settling of the excavated area. Modified stone was added on top of the back fill and compacted and graded in order to create a safe and drivable area for the client’s continued operations.
The fieldwork for the entire project was competently managed and successfully completed by Active’s Senior Foreman Jayson Richards and Tony Salange.
Voila! Project Complete.
If you suspect a UST leak or if your site requires remediation services, don’t hesitate to contact us. We strive to get the job done on time, on budget and to create a positive experience for all of our clients; leaving every project site better than we found it.
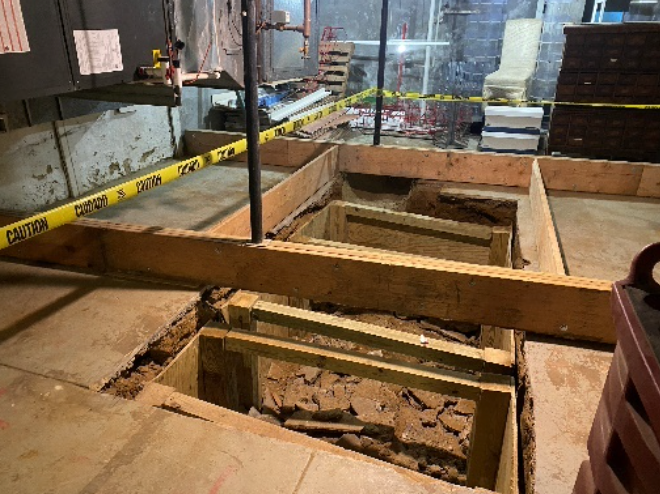
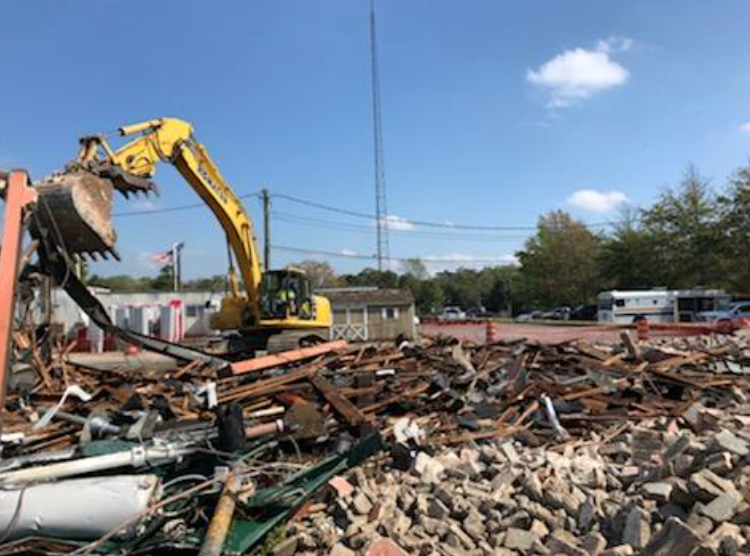
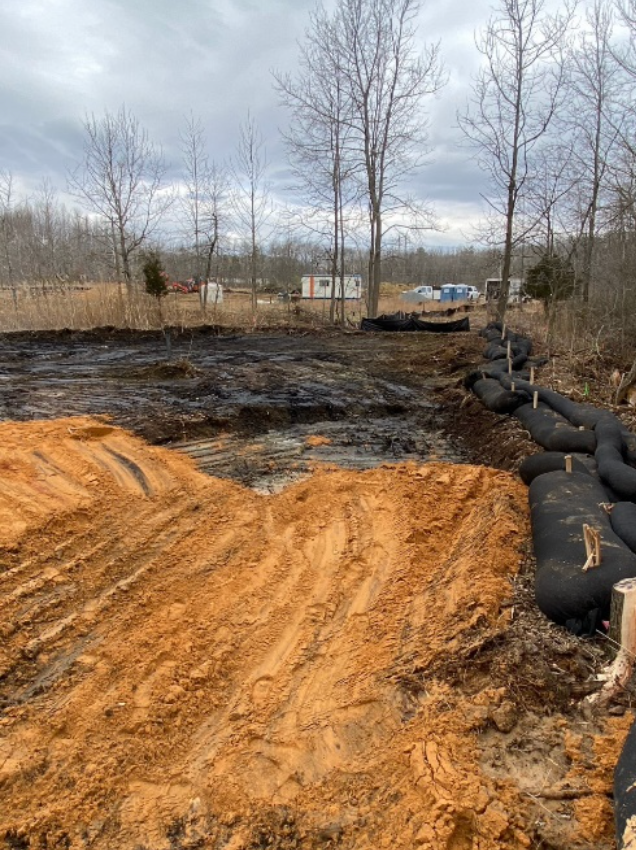
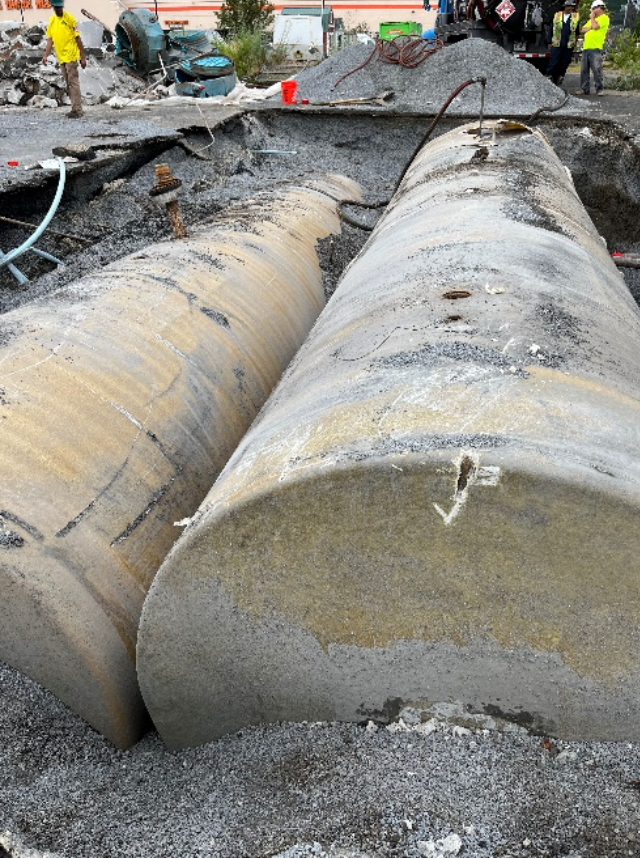